京急の鉄道模型を作っているとき書くよ。
面白い床下機器を見つけたとき載せるよ。
東杏電機製造(トウキョウデンキセイゾウ)のお知らせをするよ。
前回の記事はたしか一週間前だったでしょうか。
その間のほとんどをこの問題に取り組んでおりました。
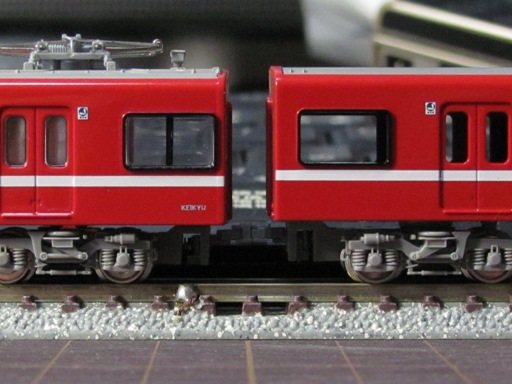
例によって先頭車ライトの点灯化の際、先頭車(左)の車高が素組(右)より0.5mmほど下がりました。
理由がなければ先頭車2両を残り6両に合わせて高くするのがラクなのですが、偶然にも下がった車高が完成品と揃っていることを発見。
これを利用しない手はないので、中間車6両も車高を下げたいと思います。
その間のほとんどをこの問題に取り組んでおりました。
例によって先頭車ライトの点灯化の際、先頭車(左)の車高が素組(右)より0.5mmほど下がりました。
理由がなければ先頭車2両を残り6両に合わせて高くするのがラクなのですが、偶然にも下がった車高が完成品と揃っていることを発見。
これを利用しない手はないので、中間車6両も車高を下げたいと思います。
もともと私は、GMや古いKATOのスナップ式の台車センターピンが大嫌いです。
今回はTOMIXやGM完成品のように、プラ円筒に台車を案内させビスで留める方式を考えてみました。
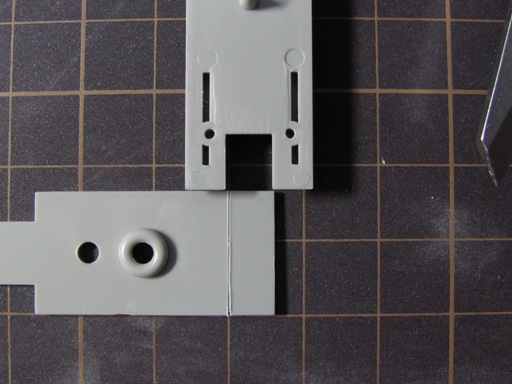
床板はキット付属のものを加工して使用します。
まず2枚構成のうち下側の先端6mmほどをカット。
切り取った小片は上側の隙間を塞ぐために使用するので、捨てないよう注意して下さい。
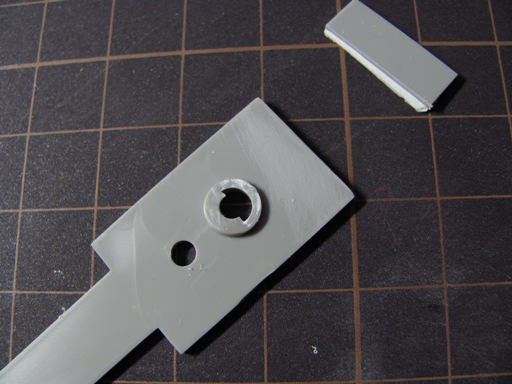
続いてオリジナルの固定穴の突起をカッターでそぎ落とします。
このとき、凹んでも良いので削り残しが無いよう気をつけます。
このパーツは裏返しで使用するので、接着を安定させるためです。
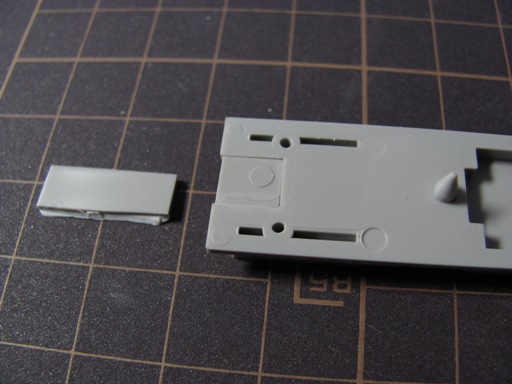
先述の通り、上側パーツ両端の切り欠きを下側から発生した小片で埋めます。
これを忘れると、完成したとき床にぽっかり穴が空き線路が見えてしまいます。
それはさすがにスリリングでよろしくないかと・・・
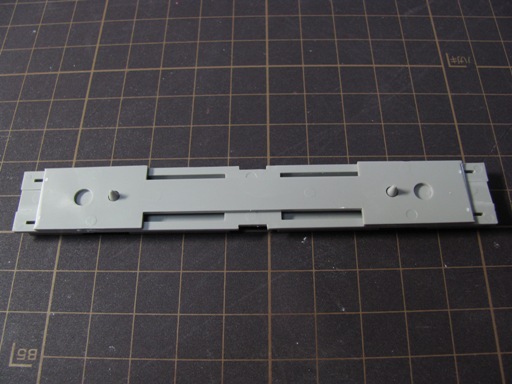
中にウェイトを仕込んで接着。
注意するすべき点は、下側パーツを裏返しにすることともう一点、台車付近を特に完全に密着させること。
共に安定性に関わるのでよく確認して下さい。
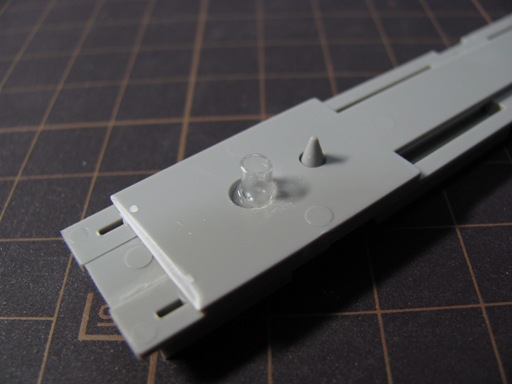
上下の固着が確認されたら、センターピンとなるプラ円筒を接着します。
使用するのはタミヤの直径3mm透明プラパイプ。
車体中心寄りへずらした位置に固定すると、台車中心間隔がGM完成品と揃います。
荷重がかかる部分なので、一度固まったらもう一度接着剤を流し込み固定を強固にします。
カットすべき長さは使用するネジの形状によって変わります。
まず長めの5mmで1両だけ完成させ、少しずつ削りながら現物合わせで最適な長さを探すとよいでしょう。
目安は、台車が走行において十分な傾きができる程度です。
このまま台車を差し込むと車高が低すぎるので、摺動する突起を取り付けます。
この突起の高さで車高が決まるため、部材選びは慎重に行います。
必要な高さは正確な1.0mm。
市販のプラ板でちょうど良いと思いきや、ノギスで厚みを測ったところ1.1mmで、試作してもやはり高さが合いません。
1/150の模型で0.1mmの差は無視できないようです。
1.1mmをヤスリで削っても所定の高さは得られますが、私は常に量産が難しい(=面倒な)方法は採らないのでNG。
複数プラ板の貼り重ねで1.0mmを探したいと思います。
大きめに切り出したプラ板のバリを取り、適量の瞬間接着剤で貼り合わせたものの中心付近を計測して組み合わせを探していきます。
――1日後
いろいろ試作してみた結果、0.3mm厚プラ板の3枚重ねがジャスト1.0mmであることを発見。
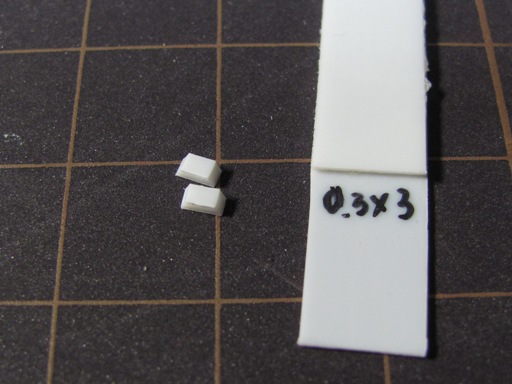
1mm幅の線に切り出しバリを除去。
それを2mmの長さにした後、バリが出ないよう写真のような台形に整えて使用します。
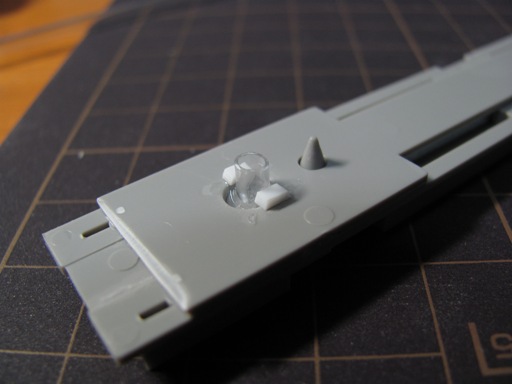
センターピンの隣へ静かに置き、ピンセットで押さえながら周囲にサラサラタイプの接着剤を流します。
水平を出すのは言わずもがな。
センターピンと比べれば破壊の恐れは低いので、接着剤は少量で十分です。
むしろ流しすぎると上面に浸透し、そのぶんの厚みが出てしまうので危険です。
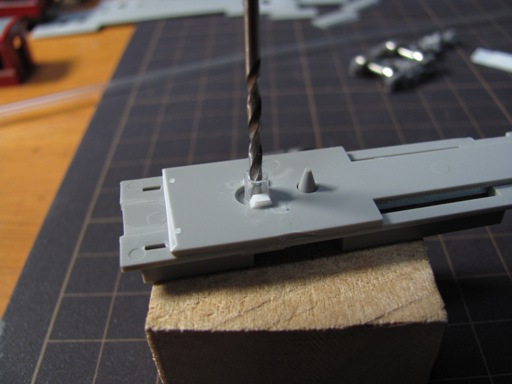
使用した接着剤が乾いたら、ドリルでビスをねじ込む穴を開けます。
センターピンのプラ円筒は内径2mmなので、ビスも2mmのものを用意。
穴明けに使用するドリルは1.7mmとしました。
眼と手先の勘で穴の中心を割り出し穴を開けます。
中心からずれると最悪の場合センターピンが割れると思いますので、慎重を期して下さい。
一度、センターピンの穴に直接ねじ切りしようと試みましたが、見事に割れました。
クリアパーツであったことが特に悪かったのかもしれません。
その考えから離れて、床板を貫通する穴を開けスチロール樹脂にねじ切りするよう思い付くまで3日かかりました。
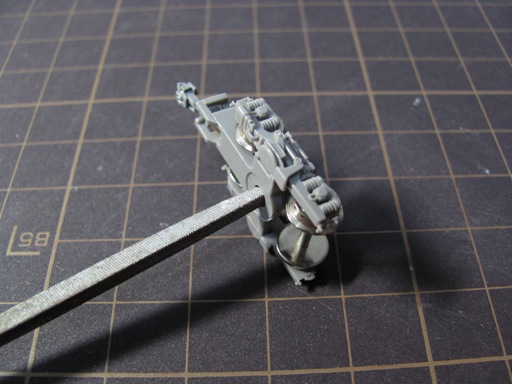
ここで台車を少々弄ります。
台車の穴の内径は3mmで、そのままだとキツすぎて3mmプラ円筒に入りません。
抵抗なく動くまでヤスリで広げます。
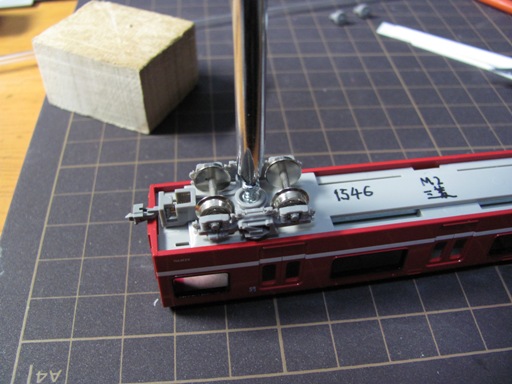
あとは組み立てるだけ。
扱い方はGM完成品とほぼ変わらないので簡単です。
ビスの長さは8mmを選びましたが、先端が車内に3mmほど飛び出したため作例では6mmでも良かったかもしれません。
それでは車体を被せ、完成後の車高を見てみましょう。
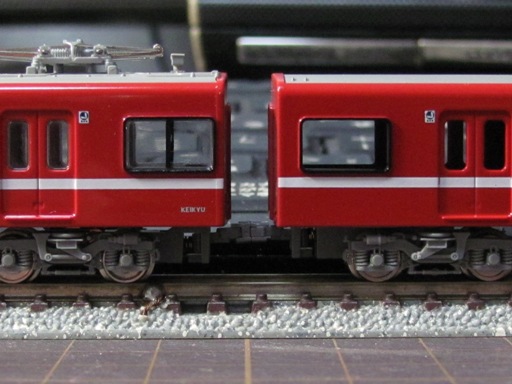
左が基準とした先頭車、右が今回改造した中間車です。
見分けがつかないでしょう?。
突起の厚みを十分に検討したお陰で、接着の際に圧着をしっかりすればかなりの高精度で完成させられます。
発生しやすい失敗が、車体の傾きやぐらつきです。
共に、1箇所だけ摺動突起の高さが異なることが原因です(2箇所も異なるのは私の作例ではありませんでした)。
水平面に置いた車両を触りながら問題のある台車および突起を特定。
目視で問題箇所と他の正常なものを比較し、高低の判定をします。
高い場合はヤスリで削り、低い場合は瞬間接着剤を盛り様子を見ます。
修正が不能なら、慎重に全ての摺動突起を撤去しやり直すのもアリでしょう。
今回はTOMIXやGM完成品のように、プラ円筒に台車を案内させビスで留める方式を考えてみました。
床板はキット付属のものを加工して使用します。
まず2枚構成のうち下側の先端6mmほどをカット。
切り取った小片は上側の隙間を塞ぐために使用するので、捨てないよう注意して下さい。
続いてオリジナルの固定穴の突起をカッターでそぎ落とします。
このとき、凹んでも良いので削り残しが無いよう気をつけます。
このパーツは裏返しで使用するので、接着を安定させるためです。
先述の通り、上側パーツ両端の切り欠きを下側から発生した小片で埋めます。
これを忘れると、完成したとき床にぽっかり穴が空き線路が見えてしまいます。
それはさすがにスリリングでよろしくないかと・・・
中にウェイトを仕込んで接着。
注意するすべき点は、下側パーツを裏返しにすることともう一点、台車付近を特に完全に密着させること。
共に安定性に関わるのでよく確認して下さい。
上下の固着が確認されたら、センターピンとなるプラ円筒を接着します。
使用するのはタミヤの直径3mm透明プラパイプ。
車体中心寄りへずらした位置に固定すると、台車中心間隔がGM完成品と揃います。
荷重がかかる部分なので、一度固まったらもう一度接着剤を流し込み固定を強固にします。
カットすべき長さは使用するネジの形状によって変わります。
まず長めの5mmで1両だけ完成させ、少しずつ削りながら現物合わせで最適な長さを探すとよいでしょう。
目安は、台車が走行において十分な傾きができる程度です。
このまま台車を差し込むと車高が低すぎるので、摺動する突起を取り付けます。
この突起の高さで車高が決まるため、部材選びは慎重に行います。
必要な高さは正確な1.0mm。
市販のプラ板でちょうど良いと思いきや、ノギスで厚みを測ったところ1.1mmで、試作してもやはり高さが合いません。
1/150の模型で0.1mmの差は無視できないようです。
1.1mmをヤスリで削っても所定の高さは得られますが、私は常に量産が難しい(=面倒な)方法は採らないのでNG。
複数プラ板の貼り重ねで1.0mmを探したいと思います。
大きめに切り出したプラ板のバリを取り、適量の瞬間接着剤で貼り合わせたものの中心付近を計測して組み合わせを探していきます。
――1日後
いろいろ試作してみた結果、0.3mm厚プラ板の3枚重ねがジャスト1.0mmであることを発見。
1mm幅の線に切り出しバリを除去。
それを2mmの長さにした後、バリが出ないよう写真のような台形に整えて使用します。
センターピンの隣へ静かに置き、ピンセットで押さえながら周囲にサラサラタイプの接着剤を流します。
水平を出すのは言わずもがな。
センターピンと比べれば破壊の恐れは低いので、接着剤は少量で十分です。
むしろ流しすぎると上面に浸透し、そのぶんの厚みが出てしまうので危険です。
使用した接着剤が乾いたら、ドリルでビスをねじ込む穴を開けます。
センターピンのプラ円筒は内径2mmなので、ビスも2mmのものを用意。
穴明けに使用するドリルは1.7mmとしました。
眼と手先の勘で穴の中心を割り出し穴を開けます。
中心からずれると最悪の場合センターピンが割れると思いますので、慎重を期して下さい。
一度、センターピンの穴に直接ねじ切りしようと試みましたが、見事に割れました。
クリアパーツであったことが特に悪かったのかもしれません。
その考えから離れて、床板を貫通する穴を開けスチロール樹脂にねじ切りするよう思い付くまで3日かかりました。
ここで台車を少々弄ります。
台車の穴の内径は3mmで、そのままだとキツすぎて3mmプラ円筒に入りません。
抵抗なく動くまでヤスリで広げます。
あとは組み立てるだけ。
扱い方はGM完成品とほぼ変わらないので簡単です。
ビスの長さは8mmを選びましたが、先端が車内に3mmほど飛び出したため作例では6mmでも良かったかもしれません。
それでは車体を被せ、完成後の車高を見てみましょう。
左が基準とした先頭車、右が今回改造した中間車です。
見分けがつかないでしょう?。
突起の厚みを十分に検討したお陰で、接着の際に圧着をしっかりすればかなりの高精度で完成させられます。
発生しやすい失敗が、車体の傾きやぐらつきです。
共に、1箇所だけ摺動突起の高さが異なることが原因です(2箇所も異なるのは私の作例ではありませんでした)。
水平面に置いた車両を触りながら問題のある台車および突起を特定。
目視で問題箇所と他の正常なものを比較し、高低の判定をします。
高い場合はヤスリで削り、低い場合は瞬間接着剤を盛り様子を見ます。
修正が不能なら、慎重に全ての摺動突起を撤去しやり直すのもアリでしょう。
この記事にコメントする
最新記事
(06/07)
(03/19)
(03/02)
(02/22)
(02/10)
(01/07)
(01/06)
(12/22)
(10/12)
(10/12)
カテゴリー
アーカイブ
ブログ内検索
プロフィール
HN:
Kojicstage
性別:
非公開
趣味:
VVVF SIV ブレーキ 台車
最新コメント
[03/01 ういすぷ]
[02/08 uuu]
[01/22 pon223]
[01/10 電機総務こたか]
[10/13 NONAME]
[10/10 NONAME]
[11/16 1367_8010]
[03/31 81SH]
[03/26 うちゅうじん]
[02/08 NONAME]
P R